We offer a range of sizes and styles of U-Joint Pullers and Bearing Cap Installers to accommodate any application.
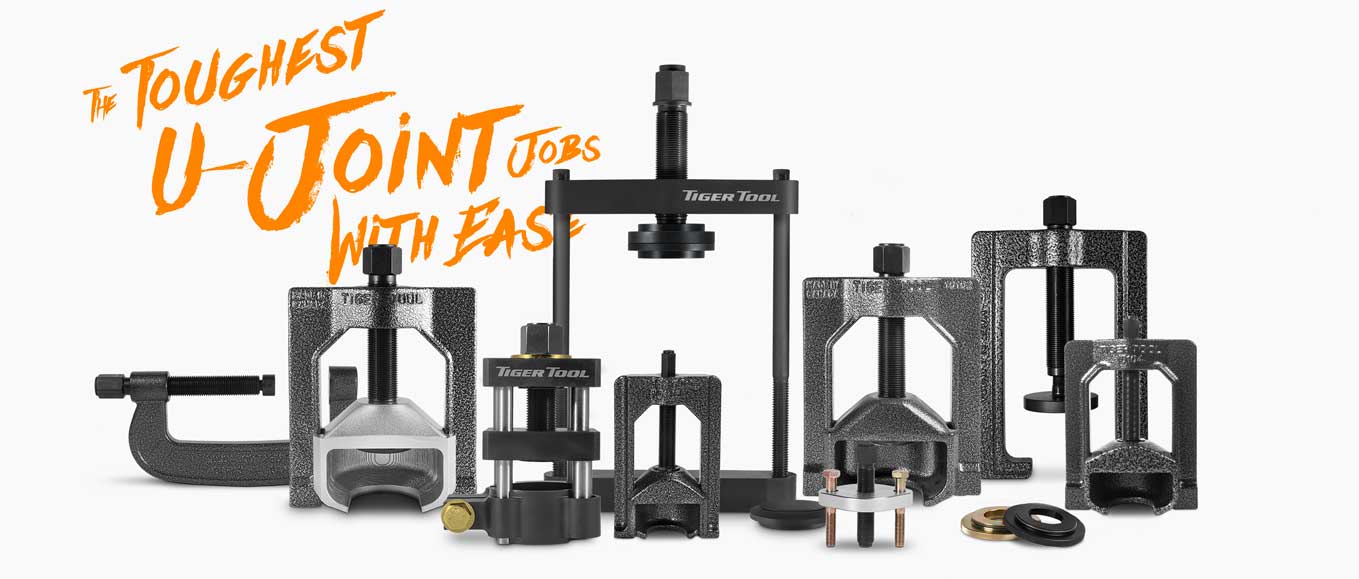
Our U-Joint Pullers and Bearing Cap Installers, when used together, ensure professional results by enabling safe disassembly and reassembly of u-joints while minimizing the risk of damage to the driveshaft and surrounding parts.
1.5” - 2.2”
Commonly found on class 6-8 transportation trucks or equipment.
Kenworth, Peterbilt, Freightliner, etc.
1.25” - 1.7”
Commonly found on class 3-5 trucks.
Isuzu NPR, Chevrolet 3500/5500, Ford F-350/550, etc.
1” - 1.25"
Commonly found on class 1-2 trucks, cars and equipment.
Ford F-150/350, Chevrolet 1500/3500, Ram 1500/3500, etc.
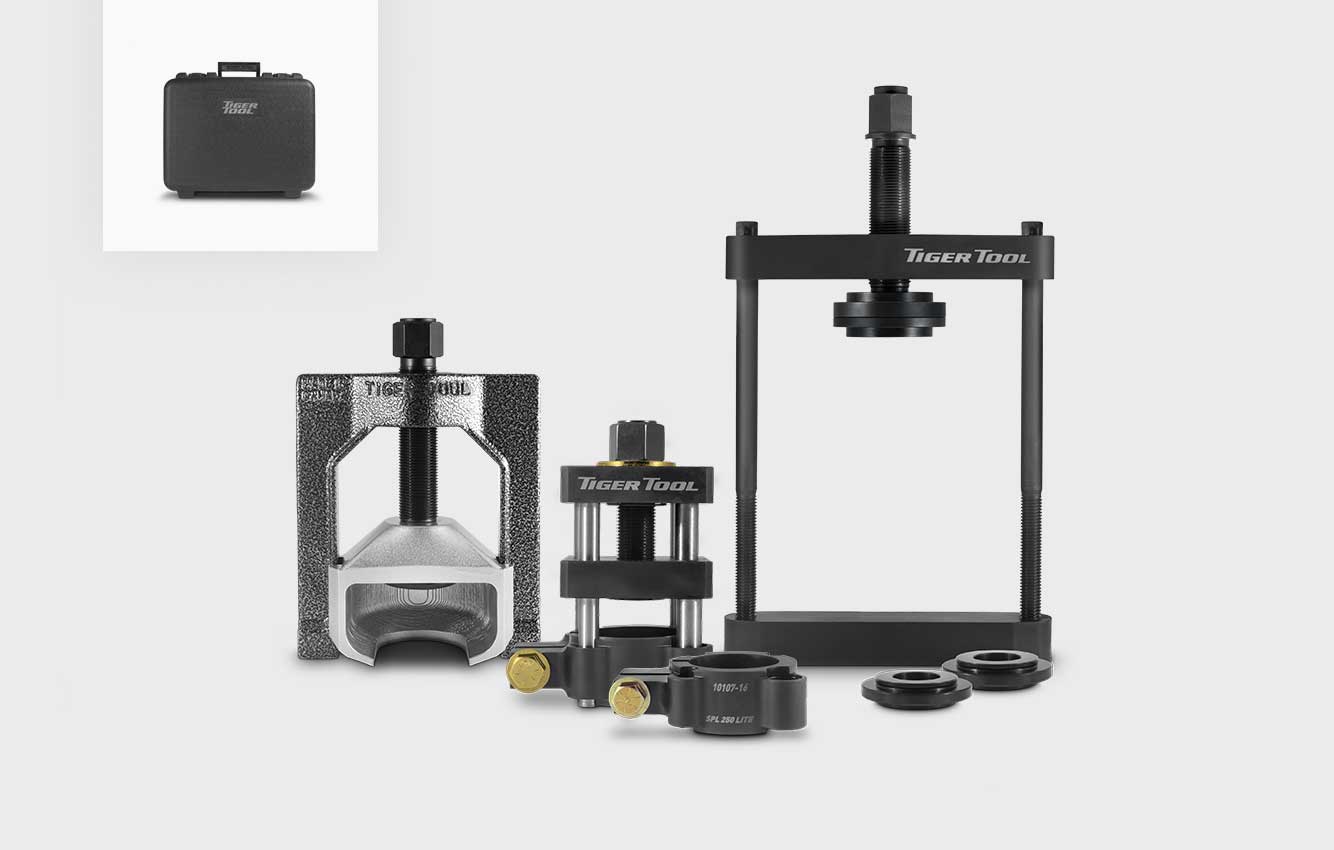
Severe Heavy Duty U-Joint Service Kit
Found on Dana/Spicer SPL 350/SFX/X, SPL 250 Lite and Meritor RPL 35 Series drivelines.
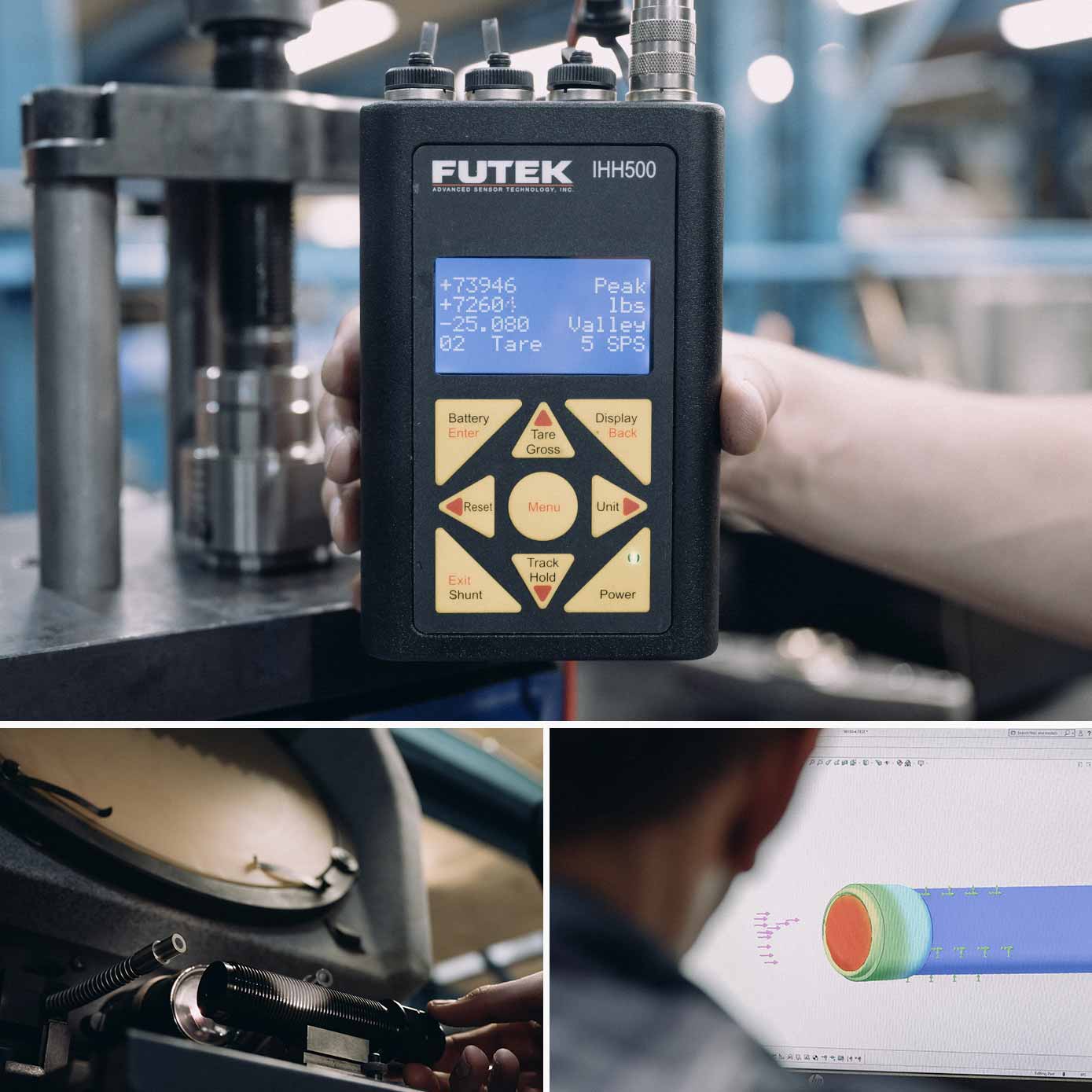
Our Forcing Screws
Our unique manufacturing and metal treatment techniques are the result of years of research and development. We use state-of-the-art equipment and advanced methods to ensure that our forcing screws are not only durable, but also able to perform under the most demanding conditions.
The process starts with selecting the highest quality materials for our screws, which are then precision machined to exact specifications. We then use a specialized metal treatment process that hardens and strengthens the screws, making them more resistant to wear and tear. This ensures that our screws can handle the high-stress and high-torque situations that are commonly encountered when dealing with stubborn, seized U-joints.
We also perform rigorous testing on our screws to ensure that they meet or exceed industry standards for strength and durability. Our manufacturing process is designed to minimize the risk of defects, so you can trust that the screws will perform as expected every time.
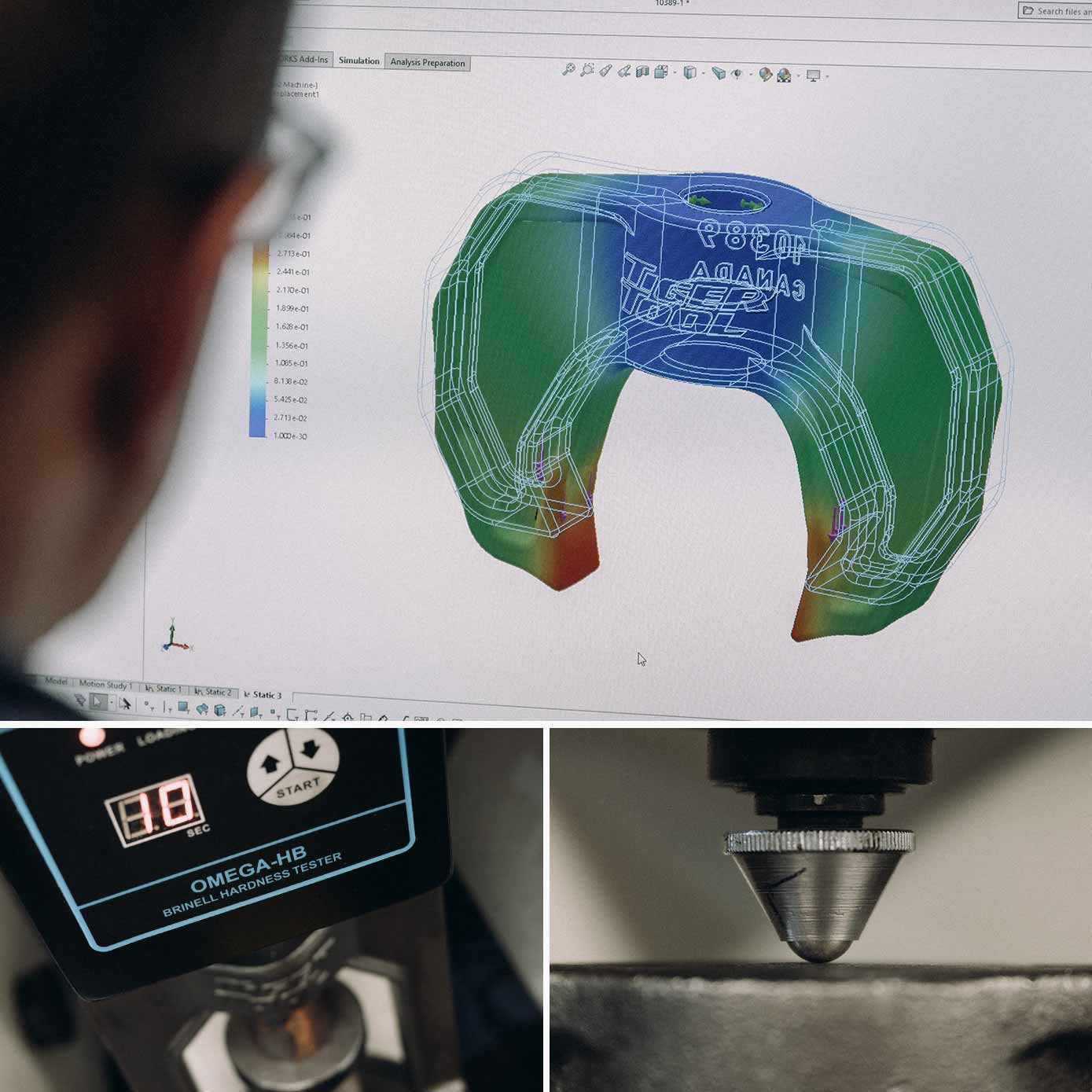
Our Castings
We utilize advanced CAD software to design highly detailed 3D models of each casting, simulating various loading conditions and stress points to ensure maximum strength and durability.
Only premium quality steel is utilized in the manufacturing process, resulting in castings that can withstand heavy usage over extended periods.
Our team of engineers and metallurgists have conducted extensive research and testing to determine the optimal composition and heat-treatment processes, as castings that are too hard may break under pressure, and those that are too soft may lose their shape under extreme loads.
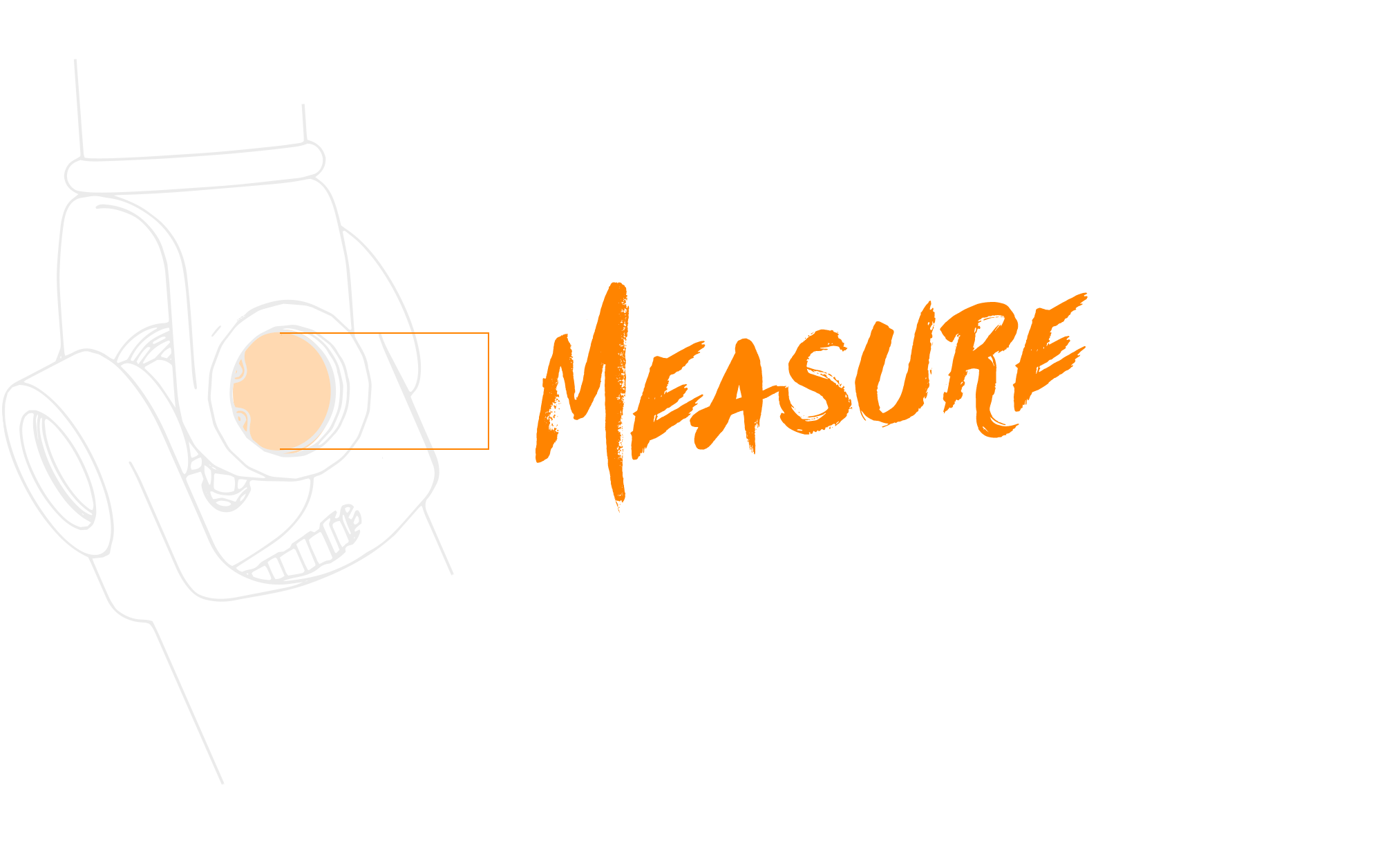